News
August 2008
Tipps für die Hochglanzlackierung
Denn nur was richtig geschwabbelt wurde, kann richtig glänzen
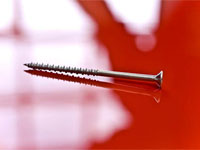
Fotos: Jordan Lacke
Hochglanz lackierte Oberflächen liegen im Trend. Warum man sich an das zunächst schwierig erscheinende Thema ruhig rantrauen kann und was man beachten sollte erklärt Jan Duzy, Anwendungstechniker beim Lackhersteller JP Coatings (Marke Jordan Lacke), der am Standort in Würzburg mehrmals im Jahr praxisorientierte Kundenschulungen mit dem Schwerpunkt »Hochglanzoberfläche leicht gemacht« anbietet:
»Zahlreiche Publikationen sind bereits über die Fertigung von polierten Hochglanzoberflächen erschienen. Doch trug die vielfältige Beschreibung des mit der Lackierung verbundenen Aufwandes eher dazu bei, dass der Handwerker verun-sichert ist und Hochglanzlackierungen entweder ablehnt, oder an spezialisierte Betriebe abgibt. Dies führt natürlich dazu, dass die Mehrzahl von Handwerkern auf solche, oft lukrative Aufträge verzichtet oder auf die Fertigung von Hochglanzoberflächen ausweicht, die nicht poliert werden. Doch führen gespritzte Hochglanzoberflächen, auch wenn sie relativ staubfrei lackiert werden, in vielen Fällen zu Beanstandungen, da sie meist dem Urteil des anspruchsvollen Kunden nicht gerecht werden, weil sie zum Beispiel sehr oft unter bestimmten Lichtverhältnissen ein unruhiges Erscheinungsbild aufweisen.

Auftrag des Isolierfüllers-
Um solche nicht zufrieden stellenden Ergebnisse aus der Produktpalette des Handwerkes streichen und eine perfekte Hochglanzoberfläche herstellen zu können, kann auf einen Polier- bzw. Schwabbelvorgang nicht verzichtet werden. Besonders für viele mittelständische Betriebe, in denen eine völlig staubfreie Lackierung nicht möglich ist, kommt die nur gespritzte Version der Hochglanzoberflächenherstellung also nicht in Frage.
Die Möglichkeit des Polierens bzw. Schwabbelns einer Lackoberfläche öffnet dem Handwerker folglich die Tür zur Teilnahme an lukrativen Hochglanzaufträgen.
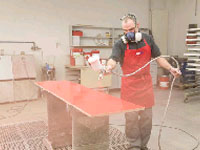
Applizieren der mehrfarbigen Schicht.
Die Erwartungen an eine hochglanzpolierte Oberfläche können bei Schiffs- und Ladenbau sowie anspruchsvollen Privatkunden sehr unterschiedlich sein. Um hier Ärger und Missverständnissen vorzubeugen, sollte bereits vor Ausfüh-rung eines Auftrages genau geprüft werden, welche Art bzw. Qualität der Kunde von der Oberfläche erwartet. Hier bietet die Anfertigung von objektbezogenen Ausfallmustern und eine vorherige Einigung über den zeitlichen Rahmen, in dem das Projekt verwirklicht werden soll, eine Garantie für eine reibungslose Abwicklung des anstehenden Auftrages.
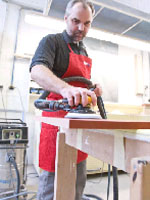
Zwischenschliff für die Endlackierung.
Um eine qualitativ hochwertige Hochglanzoberfläche, die sich durch eine dreidimensionale Formstabilität auszeichnet zu erhalten, sind besonders die Auswahl des Trägermaterials und der Lacksysteme von großer Bedeutung.
Vor Ausführung eines Auftrags sollte jedoch nicht nur eine enge Zusammenarbeit zwischen Kunden und Auftragnehmer stattfinden, sondern auch ein reger Informationsaustausch zwischen Auftragnehmer und Lacklieferanten, mit deren Hilfe in der Regel eine präzisere Auswahl des Beschichtungsmateriales getroffen werden kann. Hier kann der Handwerker auf die jahrelange Erfahrung der Lackhersteller zurückgreifen.
Hinsichtlich des Trägermaterials ist die Holzart bzw. dessen Beschaffenheit für die spätere Qualität des Werkstückes entscheidend. So eignen sich beispielsweise feinporige Hölzer wie Ahorn besser für eine formstabile Oberfläche als grob- oder mittelporige Hölzer wie z.B. Mahagoni.
Natürlich sollte auch der Bestimmungsort und die künftige mechanische Beanspruchung des Trägermaterials in die Materialauswahl mit einbezogen werden. Auch wenn z.B. eine Nussbaumoberfläche bei einem Schreibtisch sehr edel erscheint, so werden sich nach einer gewissen Zeit bei erheblicher Beanspruchung des Werkstückes Gebrauchsspuren einstellen, die den Anblick der Oberfläche beeinträchtigen. Hier kann ein aufklärendes Gespräch mit dem Auftraggeber Klarheit schaffen.

Frisch auflackierte farbige Endlackierung.
Entscheidet man sich bei der Wahl des Trägermaterials, bei pigmentierten Lacksystemen, nicht für ein Holz sondern für eine MDF-Platte, so werden in der Regel bei folierten MDF-Platten mit einer Melaminbeschichtung von ca. 120 g/m² bessere Ergebnisse bei pigmentierten Lacksystemen erzielt als bei MDF-Platten mit einer Grundierfolie ca. 80 g/m² oder rohen MDF-Platten.
Darüber hinaus sollte bei der Entscheidung über das Trägermaterial auch die Holzfeuchte berücksichtigt werden, da es bei einer zu hohen bzw. zu niedrigen, je nach Standort und dessen klimatischen Gegebenheiten, in Kombination mit Temperaturschwankungen zu einem Schwund bzw. einem Quellen des Trägermaterials und deshalb zu einer nicht vollkommen planen Oberfläche kommen kann.
Auch eine sorgfältige Auswahl der Leime darf nicht unberücksichtigt bleiben. Eine zu satt aufgetragene Leimschicht, eines zudem sich sehr stark thermoplastisch verhaltenden Leimes, kann auch noch Wochen nach der Werkstückfertigstellung zu einer unruhigen Oberfläche oder zu einem sich Abzeichnen der Leimfugen führen. Begünstigt wird dieses, wenn das Werkstück danach, extremen Temperaturschwankungen bzw. klimatischen Veränderungen ausgesetzt ist, wie es z. B. bei Verschiffungen im Container der Fall ist.
Ein weiterer wichtiger Faktor bei der Anfertigung einer Hochglanzoberfläche ist die Auswahl des richtigen Lacksystems. Hierbei kann, wie bereits erwähnt, der Lacklieferant dem Auftragnehmer mit wertvollen Informationen und Tipps zur Seite stehen.Nach detaillierten Angaben seitens des Auftragsnehmers kann eine präzise Auswahl des benötigten Materials erfolgen. Die Marke JordanLacke beispielsweise bietet hierbei mit ihrer High-Solid-Reihe schnelle und unkomplizierte 2K-PUR Lacksysteme für die Herstellung von polierten oder geschwabbelten Hochglanzoberflächen an. Diese Beschichtungssysteme mit einem Festkörperanteil von bis zu ca. 50 % erfüllen nicht nur die hohen technischen Anforderungen, die an solche Lacksysteme gestellt werden, sondern zeichnen sich gegenüber herkömmlichen Lacken zusätzlich durch ihre Effizienz und Einfachheit aus.
Schnelle Reaktionszeiten verbunden mit hohem Vernetzungsgrad verkürzen die Produktionsabläufe und Durchlaufzeiten. Lange Wartezeiten bis der Finish-Lack geschliffen und geschwabbelt werden kann gehören der Vergangenheit an. Hier genügt bereits eine Trocknung über Nacht. Durch den geringen Verbrauch können zudem die Produktionskosten enorm gesenkt werden.
In der Regel, wie auch bei Jordan Lacke üblich, wird dem Verarbeiter eine maßgeschneiderte Aufbauempfehlung zu Verfügung gestellt, in der die Abfolge der einzelnen Verarbeitungsschritte genau definiert ist.

Nassschliff mit Korn 1200 - 1500.
Die darin beschriebenen Verarbeitungsparameter wie Holzschliff, Viskositätsangaben, Applizierart, Auftragsmenge, Trocknung, Lackschliff, Polieren bzw. Schwabbeln, etc. sichern einen störungsfreien Arbeitsablauf und sind Voraussetzung für ein optimales Arbeitsergebnis.
Den letzten Schliff erhalten die lackierten Oberflächen durch den Schleif- und Poliervorgang. Hier entscheidet die sorgfältige Vorarbeit bezüglich der Materialauswahl und Lackierung über den noch zu erbringenden Aufwand und die Güte des Ergebnisses.
Je nach Sauberkeit und “Ruhe” der lackierten Oberfläche ist eine entsprechende Körnung des geeigneten Schleifpapiers für den Planschliff auszuwählen. Je unruhiger die Lackier-ung, desto gröberes Schleifpapier (600 - 800 Korn) wird zunächst eingesetzt. Eine sehr sauber gearbeitete Oberfläche hingegen kommt bereits zu Beginn des Schleifvorgangs mit einer Körnung von 1000 aus. Generell ist bei großflächigen und planen, nicht profilierten Werkstücken ein maschineller Schleifvorgang mit Flächenschleifautomaten zu empfehlen. Hiermit wird eine vollkommen plane Oberfläche gewährleistet.

Hochpolieren mit Polierpaste.
Wird ein Planschliff mit Exzenterschleifer (3mm Hub) gewählt, kann statt eines Schleifpapiers auch ein Schleifgitter verwendet werden. Diese zeichnen sich durch sehr gute Schleifergebnisse und eine sehr lange Standzeit gegenüber herkömmlichen Schleifpapieren aus.
Auch die Empfehlung bis zu welcher Körnung nass oder trocken geschliffen werden muss, bevor mit dem Polieren begonnen wird, ist umstritten. Vergleicht man die Aussagen der Lackhersteller wird sicherlich festzustellen sein, dass hier unterschiedliche Angaben gemacht werden. Zum einen Teil ist es Werkstücks bzw. lacktechnisch bedingt, zum anderen jedoch aufgrund der beim Handwerker Vorort vorzufindenden Voraussetzungen gegeben. Verfügt ein Handwerker über eine maschinelle Ausstattung die rationelle Arbeitsabläufe ermöglichen, wie z. B. geeignete Lackschleifautomaten oder einen Schwabbelautomaten, genügt hier in der Regel ein “Endlackschliff” der Körnung 1200. Verfügt hingegen ein Handwerker über solche optimalen Voraussetzungen nicht, muss der „Endschliff“ mindestens bis zu einer Körnung 1500-2000 durchgeführt werden.
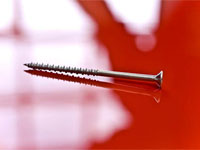
Fertige Hochglanzoberfläche.
Der Einsatz feinerer Körnungen würde zwar den Zeitauf-wand des Schwabbelvorganges erheblich reduzieren, birgt jedoch in sich die Gefahr, dass hierdurch einen nicht selten vorkommenden Kornausriss der eingesetzten Schleifpapiere oder das nicht genügende Ausschleifen einer der zuvor eingesetzten gröberen Körnungen die Polierarbeit um meh-rere Arbeitsschritte zurücksetzen würde. Hier ist es vorteilhafter, mit entsprechend abgestuften Schleifpasten zu arbeiten. Wird eine Lackierung nass ‘endgeschliffen’, wird sie sich durch den feineren Schliff, auch bei gleich eingesetzter Körnung, dem Trockenschliff gegenüber vorteilhafter absetzen. Sind jedoch die Werkstücke mit nicht lackierten Fräsungen, Bohrungen, etc. versehen, sollte hier, um das Eindringen vom Wasser in das Trägermaterial zu verhindern, generell der Trockenschliff durchgeführt werden.
Sind nun die von den Lackherstellern empfohlenen, ordnungsgemäß durchgeführten Schleifarbeiten beendet, kann mit dem Polieren begonnen werden. Hierfür eignen sich besonders gut elektronisch drehzahlregelbare Handpoliermaschinen.
Diese ermöglichen durchaus z. B. eine Küchenvorderfront oder eine exklusive Arbeitszimmereinrichtung auszupolie-ren. Elektronisch regelbare Handpoliermaschinen verhindern zudem, dass mit einer der nicht der Oberfläche ange-passten Drehzahl der Polierscheibe gearbeitet werden muss.
Eine der Oberfläche nicht angepasste und womöglich zu hohe Drehzahl der Polierscheibe führt in der Regel zu einer übermäßigen Wärmeentwicklung der Lackschichten und somit zwangsläufig zu einer Unruhe der fertig polierten Endoberfläche. Bei größeren Objekten sollte an eine Anschaffung von Schwabbelbändern, die für Langbandschleifmaschinen geeignet sind, nachgedacht werden.
Ob nun beim Einsatz der Handpolier-Maschinen, Filz oder Molton-Scheiben oder ob Schleif- und Polierpasten auf wässriger oder Petroleum Basis Verwendung finden, erfüllen bei entsprechender Sorgfalt und einer Portion mehr Selbstvertrauen alle Materialien die in der Regel an sie gestellten Erwartungen. Sehr hilfreich in diesem Zusammenhang, ist der Besuch einer Schulung, bei der erfahrene Experten mit Rat und Tat die Kunden unterstützen.«
google_ads
Diese Artikel könnten Sie auch interessieren:
Schuster creativ concepte gewinnt CNC-Olympiade
Blum bringt Anschlagsystem Easystick für Minipress-Maschinen
Freilichtmuseum verdirbt Käfern Appetit auf Fachwerk
Oberflächen-Wissen
Screenshot für 3D-Anwendungen
So teuer wie Edelparfum muss es nicht sein
Bosch sucht Profi-Tester
Türen und Fenster mit Mineralfasern dämmen
Baubeschläge in komplexen Anwendungen
Challenge von Bi-Matic