to-mac
ww-birnbaum
Hallo zusammen,
bevor der Trend vorbei ist möchte auch ich hier noch meine selbst gebaute Absaughaube präsentieren
Das Projekt hat sich über bestimmt ein Jahr hingezogen und wurde immer mal wieder nebenher vorangetrieben und weiter verbessert, so dass es nun endlich einen vorzeigbaren und finalen Stand erreicht hat.
Bis dahin musste ich mich u.a. noch mit den Themen (Metall-)Fräsen und 3D Druck auseinandersetzen um das Projekt vollenden zu können.
Los ging es mit dem gebogenem Rohr welches die Absaughaube trägt und gleichzeitig als Luftführung dient.
Dieses ist aus Edelstahl und hat einen Außendurchmesser von 70 mm und eine Wandstärke von 2 mm.
Üblich und besser wären 80 mm, aber das konnte nicht zu einem vertretbaren Preis aufgetrieben werden. Die Preise für ein Einzelstück lagen bei allen Firmen die ich angefragt habe über 150 €, Grund waren die Maschinenrüstzeiten, der Materialpreis fiel dagegen kaum noch ins Gewicht, drei Rohre wären dann auch kaum teurer gewesen. Fündig wurde ich bei einer Firma die Abgasanlagen für Autos herstellt, dort waren dann allerdings die 70mm der größte Durchmesser den sie verarbeiten konnten.
Die Verbindung zur Maschine geht über eine Aluminiumhalterung (das ist eine Motorhalterung für CNC Fräsen, gibt es günstig in verschiedenen Durchmessern bis 80mm) die wiederum an einem 60x60x3 mm Vierkantstahlrohr befestigt ist. Mit dem Klemmhebel an der Halterung kann der Absaugarm gelöst und dann ganz einfach komplett weggeschwenkt werden, für den Fall das er bei großen Werkstücken mal im Weg ist.
Die Befestigung des Parallelogramms am Rohr geschieht über zwei Aluminium Klemmstücke. Diese habe ich selber auf der Bohr-/Fräsmaschine angefertigt. Hier war die Herausforderung den Kreisausschnitt mit genau 70mm hinzubekommen. Mit einem Rundtisch hat das dann aber zu meiner Überraschung auf Anhieb funktioniert.
An den Klemmstücken sind dann die zwei Aluprofile 40x16 mm gelagert die zur Haube führen. Die Lagerung erfolgt mittels Axiallager, dadurch ergibt sich eine spielfreie und leichtgängige Lagerung.
Mit dem langen Handhebel kann die Spanhaube in der Höhe fixiert werden. Die Besonderheit hierbei ist, dass nur die Bewegung nach unten fixiert wird und nicht die Bewegung nach oben. Dadurch muss man die Höhe nur "so ungefähr" passend einstellen, am besten 1-2 cm niedriger als die Werkstückdicke, die Haube hebt sich dann über das Einlaufrad alleine auf die richtige Höhe und liegt dann genau auf dem Werkstück auf. Dies macht die Sache sicherer und optimiert die Absaugleistung.
Dieses Prinzip habe ich mir bei der SUVA Spanhaubenhalterung abgeschaut.
Bei Platten oder Brettern bis ca. 2,5 cm Dicke braucht man die Haube gar nicht anheben, sondern kann das Werkstück einfach unter der komplett abgesenkten Haube hindurchschieben - sehr sicher und komfortabel!
Zur Spanhaube selber:
Die Spanhaube habe ich mit Fusion360 in CAD konstruiert und mit dem 3D Drucker aus PETG gedruckt.
Die durchsichtige Abdeckscheibe besteht aus 4 mm starkem Polycarbonat.
Bis zum ersten gelungenen Druck war es allerdings ein langer Weg.
Ein Prototyp aus PLA hat auf Anhieb funktioniert, aber PLA ist leider nicht stabil bzw. zäh genug für das Funktionsteil. Der Druck aus PETG gestaltete sich dann wesentlich schwieriger, da die Materialspannungen beim Druck so groß wurden dass es immer wieder zu Rissen kam. Aber das war bei weitem nicht das einzige Problem..
Hier musste ich also mehrfach umkonstruieren bis es dann beim elften Versuch endlich erfolgreich war!
Viele Fehlversuche und damit einige Kilogramm PETG gingen dann irgendwann auch ins Geld..
Besonderheiten bezüglich der Funktionalität der Spanhaube:
Eine Herausforderung war, trotz der breiten Ausführung, die für Schnitte mit geschwenktem Sägeblatt ja benötigt wird, eine gute Absaugleistung zur erhalten.
Dies habe ich bisher bei keiner käuflichen Haube feststellen können, denn dort ist der Stutzen bei den breiten Hauben immer der gleiche wie für die schmalen Ausführungen und im Querschnitt zu gering. Die Aufweitung des Luftkanals innerhalb der Haube setzt dann die Strömungsgeschwindigkeit noch weiter herab so dass nicht mehr viel Saugleistung am Sägeblatt ankommt.
Bei meiner Haube ist dies anders gelöst, hier wird der Kanal verjüngt und die Strömungsgeschwindigkeit zum Blatt hin erhöht ohne jedoch zu großen Widerstand zu generieren.
Die zweite Besonderheit behebt einen weiteren Nachteil den die käuflichen breiten Hauben haben: rechts vom Sägeblatt überdecken die breiten Hauben immer viel Fläche, beim Schneiden schmaler Leisten ist dann kein Platz für z.B. einen Schiebestock.
Bei meiner Konstruktion gibt es eine Querverstellung. Durch Lösen des Sterngriffs kann die Haube nach links verschoben und so rechts vom Sägeblatt genug Platz geschaffen werden:
Das vordere Einlaufrad überdeckt übrigens auch gleich den Vorritzer. Dafür musste es jedoch ab der Hälfte etwas abgedreht werden damit das Vorritz-Sägeblatt das Rad nicht berührt und ungewollt auf Drehzahl bringt.
Hier noch weitere Impressionen:
(Sämtliche Schlauchstutzen und Adapter sind auch aus dem 3D Drucker)
Fazit: es hat (mal wieder) viel Zeit, Geld und Nerven gekostet - aber es hat sich gelohnt!
Die Absaugleistung ist sehr gut, die Optik passt und die Stabilität auch: man kann auch mit viel Kraft, wenn man seitlich auf die Haube drückt, den 5-10 mm großen Freiraum zwischen der Abdeckscheibe und dem Sägeblatt nicht zudrücken. Es besteht also keine Gefahr dass die schöne Haube ins Sägeblatt gerät.
Naja, eigentlich wollte ich ja nicht mehr so viel an den Maschinen rumbasteln, sondern mehr mit ihnen arbeiten. Aber irgendwie kann ich einfach nicht anders..
Und in diesem Fall war der Eigenbau ja auch nochmal gerechtfertigt - es gibt hierzu einfach keine käufliche Lösung die alle meine Wünsche und Ansprüche erfüllt hätte!
Viele Grüße!
Tobias
bevor der Trend vorbei ist möchte auch ich hier noch meine selbst gebaute Absaughaube präsentieren
Das Projekt hat sich über bestimmt ein Jahr hingezogen und wurde immer mal wieder nebenher vorangetrieben und weiter verbessert, so dass es nun endlich einen vorzeigbaren und finalen Stand erreicht hat.
Bis dahin musste ich mich u.a. noch mit den Themen (Metall-)Fräsen und 3D Druck auseinandersetzen um das Projekt vollenden zu können.
Los ging es mit dem gebogenem Rohr welches die Absaughaube trägt und gleichzeitig als Luftführung dient.
Dieses ist aus Edelstahl und hat einen Außendurchmesser von 70 mm und eine Wandstärke von 2 mm.
Üblich und besser wären 80 mm, aber das konnte nicht zu einem vertretbaren Preis aufgetrieben werden. Die Preise für ein Einzelstück lagen bei allen Firmen die ich angefragt habe über 150 €, Grund waren die Maschinenrüstzeiten, der Materialpreis fiel dagegen kaum noch ins Gewicht, drei Rohre wären dann auch kaum teurer gewesen. Fündig wurde ich bei einer Firma die Abgasanlagen für Autos herstellt, dort waren dann allerdings die 70mm der größte Durchmesser den sie verarbeiten konnten.

Die Verbindung zur Maschine geht über eine Aluminiumhalterung (das ist eine Motorhalterung für CNC Fräsen, gibt es günstig in verschiedenen Durchmessern bis 80mm) die wiederum an einem 60x60x3 mm Vierkantstahlrohr befestigt ist. Mit dem Klemmhebel an der Halterung kann der Absaugarm gelöst und dann ganz einfach komplett weggeschwenkt werden, für den Fall das er bei großen Werkstücken mal im Weg ist.
Die Befestigung des Parallelogramms am Rohr geschieht über zwei Aluminium Klemmstücke. Diese habe ich selber auf der Bohr-/Fräsmaschine angefertigt. Hier war die Herausforderung den Kreisausschnitt mit genau 70mm hinzubekommen. Mit einem Rundtisch hat das dann aber zu meiner Überraschung auf Anhieb funktioniert.
An den Klemmstücken sind dann die zwei Aluprofile 40x16 mm gelagert die zur Haube führen. Die Lagerung erfolgt mittels Axiallager, dadurch ergibt sich eine spielfreie und leichtgängige Lagerung.
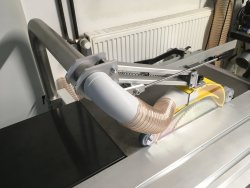

Mit dem langen Handhebel kann die Spanhaube in der Höhe fixiert werden. Die Besonderheit hierbei ist, dass nur die Bewegung nach unten fixiert wird und nicht die Bewegung nach oben. Dadurch muss man die Höhe nur "so ungefähr" passend einstellen, am besten 1-2 cm niedriger als die Werkstückdicke, die Haube hebt sich dann über das Einlaufrad alleine auf die richtige Höhe und liegt dann genau auf dem Werkstück auf. Dies macht die Sache sicherer und optimiert die Absaugleistung.
Dieses Prinzip habe ich mir bei der SUVA Spanhaubenhalterung abgeschaut.
Bei Platten oder Brettern bis ca. 2,5 cm Dicke braucht man die Haube gar nicht anheben, sondern kann das Werkstück einfach unter der komplett abgesenkten Haube hindurchschieben - sehr sicher und komfortabel!

Zur Spanhaube selber:
Die Spanhaube habe ich mit Fusion360 in CAD konstruiert und mit dem 3D Drucker aus PETG gedruckt.
Die durchsichtige Abdeckscheibe besteht aus 4 mm starkem Polycarbonat.
Bis zum ersten gelungenen Druck war es allerdings ein langer Weg.
Ein Prototyp aus PLA hat auf Anhieb funktioniert, aber PLA ist leider nicht stabil bzw. zäh genug für das Funktionsteil. Der Druck aus PETG gestaltete sich dann wesentlich schwieriger, da die Materialspannungen beim Druck so groß wurden dass es immer wieder zu Rissen kam. Aber das war bei weitem nicht das einzige Problem..
Hier musste ich also mehrfach umkonstruieren bis es dann beim elften Versuch endlich erfolgreich war!

Viele Fehlversuche und damit einige Kilogramm PETG gingen dann irgendwann auch ins Geld..
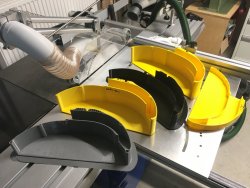

Besonderheiten bezüglich der Funktionalität der Spanhaube:
Eine Herausforderung war, trotz der breiten Ausführung, die für Schnitte mit geschwenktem Sägeblatt ja benötigt wird, eine gute Absaugleistung zur erhalten.
Dies habe ich bisher bei keiner käuflichen Haube feststellen können, denn dort ist der Stutzen bei den breiten Hauben immer der gleiche wie für die schmalen Ausführungen und im Querschnitt zu gering. Die Aufweitung des Luftkanals innerhalb der Haube setzt dann die Strömungsgeschwindigkeit noch weiter herab so dass nicht mehr viel Saugleistung am Sägeblatt ankommt.
Bei meiner Haube ist dies anders gelöst, hier wird der Kanal verjüngt und die Strömungsgeschwindigkeit zum Blatt hin erhöht ohne jedoch zu großen Widerstand zu generieren.
Die zweite Besonderheit behebt einen weiteren Nachteil den die käuflichen breiten Hauben haben: rechts vom Sägeblatt überdecken die breiten Hauben immer viel Fläche, beim Schneiden schmaler Leisten ist dann kein Platz für z.B. einen Schiebestock.
Bei meiner Konstruktion gibt es eine Querverstellung. Durch Lösen des Sterngriffs kann die Haube nach links verschoben und so rechts vom Sägeblatt genug Platz geschaffen werden:

Das vordere Einlaufrad überdeckt übrigens auch gleich den Vorritzer. Dafür musste es jedoch ab der Hälfte etwas abgedreht werden damit das Vorritz-Sägeblatt das Rad nicht berührt und ungewollt auf Drehzahl bringt.
Hier noch weitere Impressionen:
(Sämtliche Schlauchstutzen und Adapter sind auch aus dem 3D Drucker)



Fazit: es hat (mal wieder) viel Zeit, Geld und Nerven gekostet - aber es hat sich gelohnt!
Die Absaugleistung ist sehr gut, die Optik passt und die Stabilität auch: man kann auch mit viel Kraft, wenn man seitlich auf die Haube drückt, den 5-10 mm großen Freiraum zwischen der Abdeckscheibe und dem Sägeblatt nicht zudrücken. Es besteht also keine Gefahr dass die schöne Haube ins Sägeblatt gerät.
Naja, eigentlich wollte ich ja nicht mehr so viel an den Maschinen rumbasteln, sondern mehr mit ihnen arbeiten. Aber irgendwie kann ich einfach nicht anders..
Und in diesem Fall war der Eigenbau ja auch nochmal gerechtfertigt - es gibt hierzu einfach keine käufliche Lösung die alle meine Wünsche und Ansprüche erfüllt hätte!
Viele Grüße!
Tobias